Book Now!
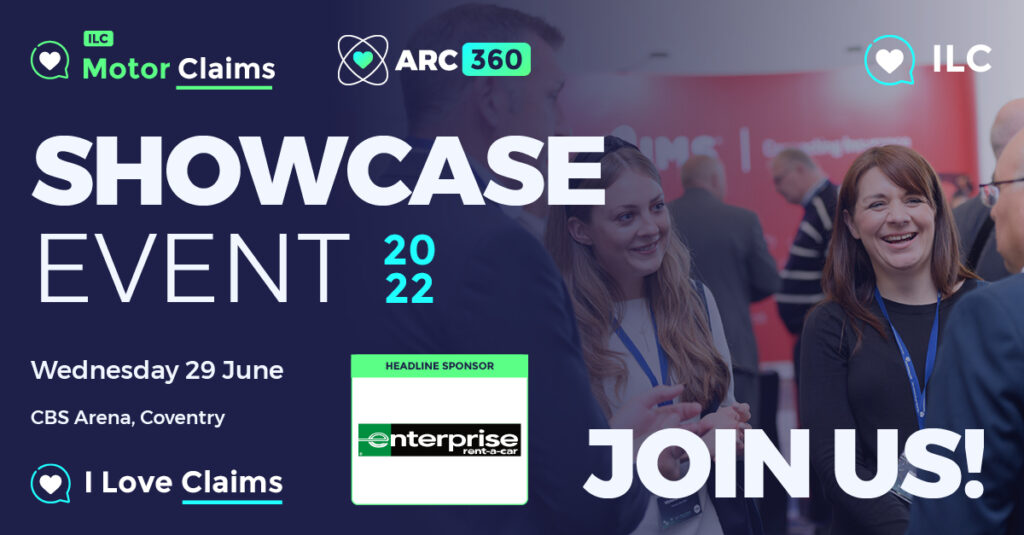
Momentum builds for Motor Showcase Event
ILC and ARC360’s inaugural Motor Showcase Event continues to gain traction with the industry showing its support for the new experience.
Headline sponsored by Enterprise, the event will provide host of engaging initiatives including the ‘next generation’ meet and greet session; a fully immersive exhibition arena; a Partner Showcase stage; and the main auditorium keynote stage.
The skills crisis laid bare
While everyone appreciates that there is a skills crisis in the automotive repair sector, some of the statistics cited during the most recent webinar hosted by ARC360, in association with ILC, will have made grim reading.
It was revealed during Episode 4, Series 4, People & Skills, that there has been a 25% increase in vacancies in recent years, with up to 15 in every 100 roles now unfilled.
Feature Interview: Stuart Sandell, Enterprise Holdings
As the automotive industry evolves both through technological and societal change, so too must its workforce in terms of demographic and skills.
Here, we speak to Stuart Sandell, AVP Sales for Insurance Replacement UK & Ireland at Enterprise Holdings, about the changing face of people and skills in the sector.
Aviva partners with Tractable to enhance AI capabilities
Aviva has announced a new agreement with Tractable to introduce artificial intelligence (AI) technology to its motor claims process.
Aviva expects that by implementing this solution it will be able to quickly and accurately complete remote assessment of repair estimates while also increasing consistency of diagnosis.
S&G increases northern footprint
S&G Response has opened new offices in Halifax as it continues its expansion into the north of the country.
Managing Director Andy Whatmough said, “Halifax is a thriving northern town with an exceptionally strong insurance community. We have been looking to increase our geographical footprint since the end of the Covid-19 period and this provides the ideal opportunity to expand our service delivery capability and recruit further talented people into our culture.”
Repair complexity leaving aftermarket behind
The cost and skills required to repair modern vehicles have not been fully appreciated throughout the sector, meaning some jobs could potentially be performed incorrectly and repairers are not being properly renumerated.
That is the verdict of Chris Brightmore, CEO of Chartwell Group, which is the country’s leading supercar repair centre.
sopp+sopp introduces AI to claims management
Accident management company sopp+sopp will introduce an automated FNOL service for commercial fleets after agreeing a deal to deploy technology developed by video telematics specialist VisionTrack.
VisionTrack uses artificial intelligence and computer vision to validate driver welfare, streamline claims handling and reduce insurance costs.
Commercial director of sopp+sopp Callum Langan said, “We will gain faster, more accurate reporting, enabling us to reduce unreported incidents and safeguard driver wellbeing.”
Spanesi adds 3D designs to portolio
Bodyshop equipment manufacturer Spanesi has enhanced its offering after agreeing a partnership with EC Design, which specialises in 3D layouts that help repairers maximise space and ensure smooth workflows through the workshop.
Driven reports strong quarterly results
US-based automotive services provider Driven Brands has reported a 42% uptick in revenues in the first quarter of the year compared to the same period of 2021.
Revenues increased to $468.3m, while net income was $34.4m in the first quarter, during which time the company also added 114 new net stores.
President and CEO Jonathan Fitzpatrick said, “Driven Brands posted strong first quarter results despite a challenging macroeconomic landscape. Our scale and sophistication allow us to navigate continued supply chain challenges and an accelerating inflationary environment.”
Lucid secures substantial Saudi order
Electric car manufacturer Lucid Group has signed a deal to deliver up to 100,000 vehicles to Saudi Arabia in the next 10 years. The initial order is for 50,000 vehicles with an option to double that number over the same time period.
Delivery of 1,000 to 2,000 vehicles per year will begin no later than the second quarter of 2023, with that number rising to between 4,000 and 7,000 from 2025.
Peter Rawlinson, Lucid’s CEO and CTO, said, “Delivering up to 100,000 Lucid electric vehicles in Saudi Arabia represents another pivotal moment in our acceleration of sustainable transportation worldwide.”
Register Now…
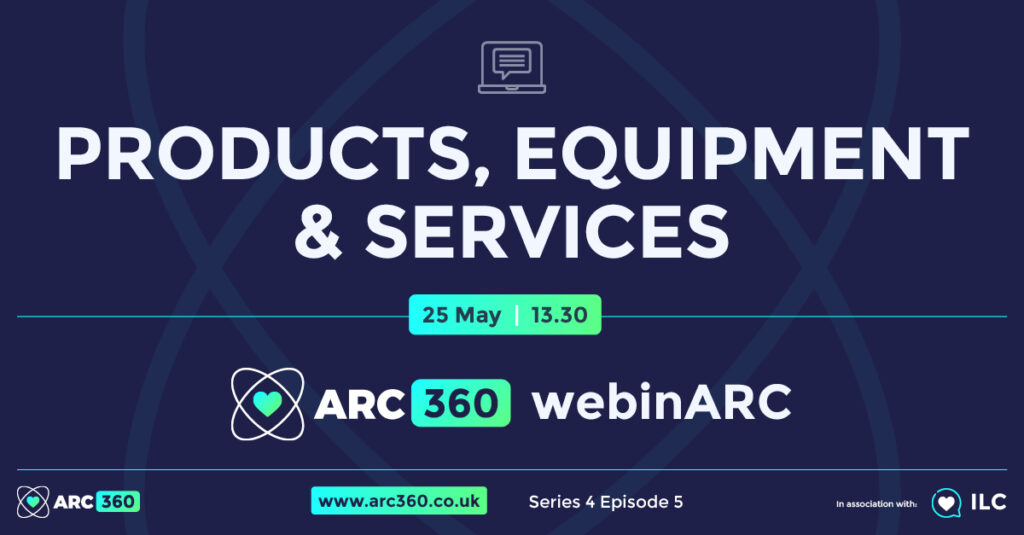
webinARC – products, equipment & services
1.30pm Wednesday 25 May
In this webinARC we explore the latest developments in repair products, equipment and services.