No short-term solution to supply disruption
Underlining the supply chain crisis currently facing the industry, an online poll during the most recent ARC360 webinar found that 73% of respondents said they are experiencing delays in parts supply on a daily basis.
A further 27% said the challenge was intermittent, with not a single respondent saying that it was business as usual when it comes to receiving the parts necessary to complete repairs.
Feature interview: Michael Golding, LV=
The relationship between companies and their supply chains is evolving. Previously transactional and sometimes even adversarial, peace is breaking out as the industry adopts a more collaborative stance to tackle current challenges.
Here we speak to Michael Golding, LV= Network Manager, to find out what impact the pandemic had on supply and how its relationship with its repair network has changed.
A sector at crossroads
A number of factors have taken the sector to a crossroads but, with so many different paths ahead, it appears more like a junction.
That was the verdict of a fascinating panel debate at the inaugural Motor Claims Showcase event which took place the CBS Arena, Coventry on 29 June.
Copart collaborates with training academy
Copart has agreed a new collaboration with Bridge Automotive Academy to support its training programme.
It will loan three cars per year to the academy to help trainees secure their IMI VDA accreditation.
Komoo set to open new site
Komoo, which provides repair services exclusively to the vehicle rental and fleet sectors, is opening a new site in Weston-Super-Mare in August.
The team behind Komoo has over 50 years’ experience in the body repair industry as well as 45 years combined experience in car rental and mobility.
Fix Auto Cheltenham quadruples capacity
Fix Auto Cheltenham’s new state-of-the-art site is open for business following a £400,000 investment from owners Kieran Humphries and Andrew Emery.
The repair centre now has four times the workspace than the previous site and, once fully operational following a recruitment drive to double the workforce, will have the capacity to repair more than 250 vehicles a month.
LV=GI secures green parts supply with Synetiq deal
LV= GI has announced a new agreement with Synetiq to increase the use of green parts in repair. It believes this will help it achieve its sustainability goals.
As part of the deal, which has been announced following a pilot initiated in 2021, LV= will now have greater access to recycled parts such as doors, lights, body panels, and major mechanical parts.
DLG Auto Services EV ready
Direct Line Group Auto Services has secured its EV Ready certification from Thatcham Research.
Jennifer Wright, Customer Service Advisor, said, “The training we received was very much needed for our own safety when working with these vehicles. It was a good training session and gave us all a full insight to the safety side of high voltage vehicles.”
RWC names new development director
RWC has appointed Matt Mardell into the new role of Business Development Director. He joins from AutoRestore, where he was Head of Operations.
S&G doubles commitment to mental health
S&G Response has doubled the number Mental Health First Aiders within the business.
Alicia Derby and Michael Bridge have both recently completed their training to join Dan Crinson and Alasdair Breed on the team.
With honours
Jason Lea, Strategic Account Manager at BASF plc UK & Ireland Automotive Refinish has earned a first-class honours degree in Business and Law from the University of Portsmouth.
VMs turn attention to insurance as a FoD
Vehicle manufacturers are increasingly moving into the insurance arena, with GM hoping to generate $6bn in insurance revenues by 2030 and Stallantis targeting up to $20bn in additional revenue by the same year.
This is part of a much wider strategic shift to offer ‘features on demand’ (FoD), to create additional revenue streams.
ARC360 Podcast episode 23: Chris Brightmore, Chartwell Group
In this episode, we speak with Chris Brightmore, CEO at super brand vehicle repair operation Chartwell (Derby) Ltd who provides an insight into business – from how it all began and working with some of the world’s leading vehicle marques, to impacts of the pandemic and what the future might hold.
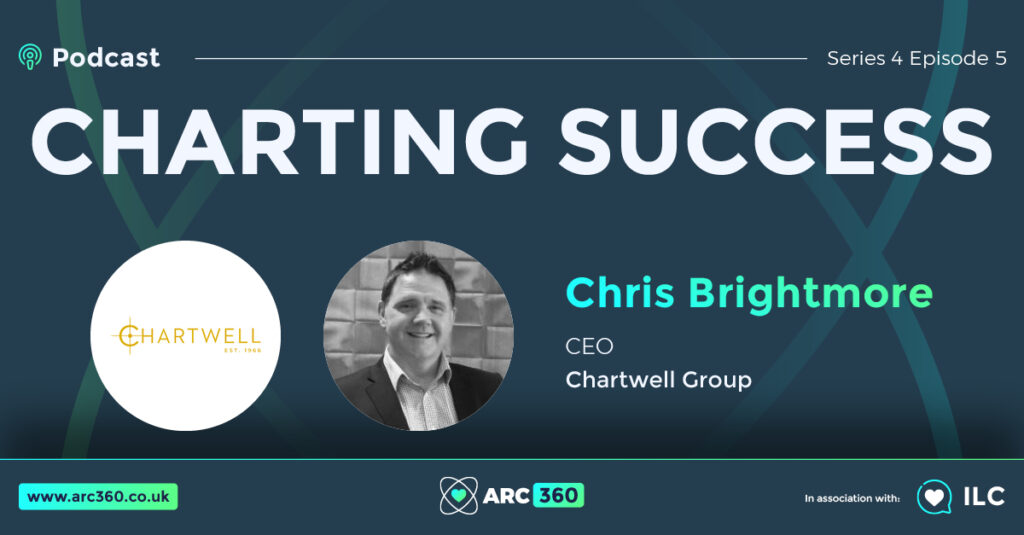