Listen up…
In the latest episode of the ARC360 podcast, we catch up with Phill Blowers, commercial director at Indasa Abrasives who offers an overview of his 35 years in the industry. He also shares his passion for cycling and reveals how he’s mixing work with pleasure by organising a charity bike ride in support of industry charity AutoRaise.
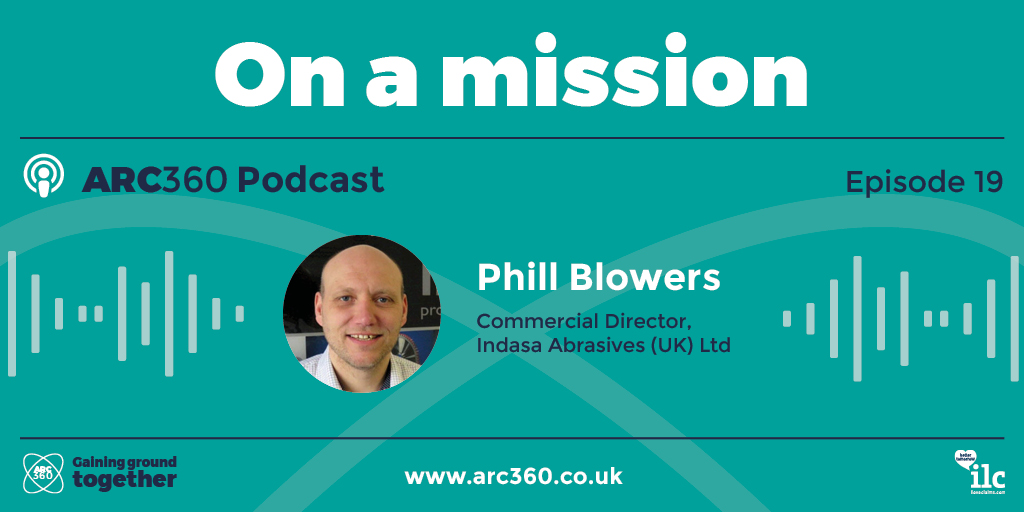
CAPS sees volumes dip for July
Claims volumes reduced by three per cent month-on-month according to the CAPS Claims Analysis report for July.
July’s unique claims figure stood at 79% of ‘pre-pandemic’ levels, compared to the 82% reported for June.
Regionally, only the East Midlands and Scotland showed uplifts in claims volumes.
Prasco UK develops smart parts App
Prasco UK has developed an App for smartphone and tablet users to speed up and make the replacement parts ordering process as seamless as possible.
Believed to be the first of its kind for the industry, the free-to-download App, which has been developed for both OS – or Apple – and Android operating systems, provides registered users with instant access to 150,000 parts currently held on site at the company’s main distribution hub in Thorne, near Doncaster.
Claims costs expected to keep climbing
The overwhelming majority of the automotive incident repair sector expects claims cost to continue rising in the next year.
Costs have risen sharply in recent years, driven up by increasing technology in vehicles and the rising price of parts, but results of a new survey suggest that most believe we are still some way short of the peak.
The second Great British Motor Claims Survey, hosted by ILC/ARC360, asked stakeholders if they expected accident claims cost to continue rising in the next year. A staggering 84% said yes, with a further five per cent unsure. Only 11% of respondents said they thought further rises were unlikely.
ABI: motor insurance at five-year low
The average price motorists are paying for their motor insurance now stands at a five year low according to the ABI’s latest Motor Insurance Premium Tracker.
The ABI’s latest Tracker for the second quarter highlights that: the average price paid for comprehensive motor insurance in the second quarter of this year was £430 – the lowest in just over five years, since Q1 2016. In the first six months of 2021 the average motor premium fell by £38.
NBRA updates tyre price guide
The NBRA has worked with Kwik Fit to update the Tyre Insurance Price Guide to ‘allow bodyshops to once again make a margin from fitting tyres where appropriate’.
Chris Weeks, Director of the National Body Repair Association (NBRA), explained, “For many years the Kwik Fit Tyre Insurance Price Guide has been the accepted insurance standard that bodyshops have been required to use for the tyre charge out price on insurance invoices. The price list had remained unchanged since 2017 leaving bodyshops in many cases forced to charge less for tyres than they were paying themselves.”
Fix Auto franchisee selects imageproof approach
Service Certainty’s imageproof Pro has been selected by Fix Auto Bury St Edmunds as its customer imaging solution.
Service Certainty imageproof Pro offers a national network of more than 4,000 professional photographers to capture high quality images of vehicle damage from the customer’s location of choice. The service helps promote more flexible working and process efficiency.
ARC360 special – The model technician: who is tomorrow’s prototype?
More than 100 years ago a single innovation accelerated production times of the Model T from 12 hours to 93 minutes.
The innovation in question was a moving assembly line, and as well as changing the entire landscape of manufacturing across multiple industries, it also changed the jobs within automotive manufacturing and the associated skill sets that were required.
In many ways a similarly seismic shift is happening now with advanced driver assistance systems (ADAS), digitalisation and electrification – new technology is replacing old; new processes are being introduced; and new job roles are being created within the workshop, or, at least, existing job roles are changing.
AXA launches STeP claims solutions
AXA has launched STeP, a digital claims solution set to transform the insurer’s online offering and provide more choice for its motor insurance customers.
The new solution, developed inhouse by AXA, sees the insurer expand its digital capabilities beyond electronic notification into a self-serve, end-to-end digital claims experience.
AXA’s Direct Motor and Swiftcover customers can notify and track a claim online and, for certain types of claims, the journey is also automatically integrated with AXA’s suppliers who will then help them with the repair or replacement of their vehicle depending on the type of damage.
Changes in motor highlighted by DLG
Direct Line Group’s gross written premiums reduced by 1.5% for H1 2021 as continued growth in Commercial, Home and Green Flag Rescue was offset by declines in Motor and Travel.
In the insurer’s half year report 2021, Penny James, CEO of Direct Line Group, stated: “In Motor we saw claims frequency remain below normal levels, fewer new car sales and a reduction in new drivers entering the market. These factors were strongest in Q1 and have started to reverse in Q2 at the same time as motor market premium stabilised.”
Meanwhile, DLG is one of seven major UK companies to have pledged to work together with government to help accelerate the mass adoption of electric vehicles (EVs) across the UK.
Volvo rewards 2020 High Achiever winners
Volvo has presented its 2020 High Achiever awards with Volvo Cars Poole and Poole Accident Repair Centre taking the overall title for the second consecutive year.
The annual competition highlights Volvo’s most successful retailer/bodyshop relationships by region with one overall winner.
The winners of the 2020 awards are:
Region One – Lookers Colchester & Chaplane ARC
Region Two – Stoneacre Chesterfield & Burrows Doncaster
Region Three – Marshall Derby & Fix Auto Nottingham
Region Four – Brindley Wolverhampton & Shorade ARC / Johnson Gloucester & MG Cannon
Region Five – Donalds Garage Ipswich & DJ Mackenzies Ltd
Region Six – Volvo Cars North London & AD Williams High Wycombe
Region Seven – Volvo Cars Poole & Poole ARC
Region Eight – Snows Winchester & Snows Accident Repair Centre
Registrations down for July
July’s new car registrations fell by -29.5% to 123,296 units, according to the latest figures from the Society of Motor Manufacturers and Traders (SMMT).
The decline was artificially heightened by comparison with the same month last year, when registrations rose dramatically as showrooms enjoyed a full month’s operation following the first 2020 lockdown.
However, the July performance was down -22.3% on the average recorded over the past decade, as the ongoing semiconductor shortage and the ‘pingdemic’ impacted on both supply and demand.
The light commercial vehicle (LCV) market saw its first decline since December 2020 as July registrations fell -14.8%. The month’s performance was a -4.0% decline compared to the pre-pandemic five-year average.
Indasa charity ride open for entries
Entries for Indasa’s virtual charity bike ride are now open.
The 100km virtual ride, allowing participants to join in their local areas, takes place on 25 September. All monies raised will support to the work carried out by AutoRaise in promoting the dynamic vehicle repair industry as a viable and rewarding career choice for young people.
asTech backs Greener Bodyshop Awards
asTech, a Repairify company, is sponsoring the Outstanding Support for Bodyshops category in the NBRA Greener Bodyshops Awards.
Richard Taylor, asTech European business development director, said, “Our sponsorship of the NBRA Greener Bodyshops Awards reinforces our commitment to assist shops through high levels of service while being conscious of the environmental consequences of our solutions. By enabling bodyshops and SMR centres to reduce the movement of vehicles, we are helping them decrease their carbon footprint at the same time as conducting safe and accurate repairs.”
Cazoo brings refurbishment inhouse as rapid growth continues
Cazoo has brought its vehicle refurbishment in-house as it continues its rapid growth which saw sales increase by 429% to 10,692 in Q2 2021.
Alex Chesterman OBE, Founder & CEO of Cazoo, commented, “Our rapid growth trajectory continued in Q2 with record revenues of around £141 million, up 605% year on year, as consumers embraced the selection, transparency and convenience of buying cars entirely online.”
He continued, “During the quarter, we brought our vehicle refurbishment in-house and now have five vehicle preparation centres in operation across the UK, giving us a significant infrastructure advantage and complete control of our extensive UK-wide reconditioning and logistics operations.”
The business has also launched a new car subscription service offering both new and used cars with the option to purchase, finance or subscribe, all entirely online.
Ben introduces Big Breakfast fundraiser
Automotive industry charity, Ben, has launched its first ever Big Breakfast fundraiser in October.
The event runs for a week, starting on 4 October and ending on World Mental Health Day, 10 October.
Host a breakfast any day during that week and bring, bake, make and sell breakfast to raise money to support Ben’s work in the industry. Those hosting Ben’s Big Breakfast can also raffle a Ben bear to fundraise.
To find out more and sign up, click here.
Save the date…
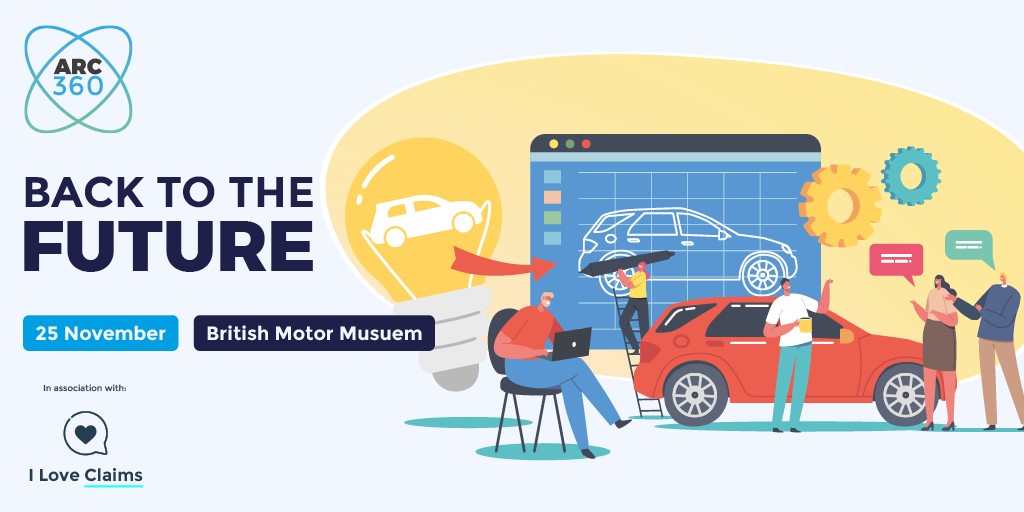
ARC360 – Back to the Future – sees a welcome return to physical events on Thursday 25 November at the British Motor Museum, Warwickshire.
Offering an event experience to remember – including plenty of exciting ARC360 initiatives – the day will focus on just what the past means for the future of the industry.